Le développement des sciences a permis des avancées importantes notamment dans l’élaboration et la synthèse de nouveaux matériaux. Cette période voit également le développement de pigments de synthèse en remplacement de minéraux toxiques.
Utilisation des minéraux et des roches dans les activités humaines du XVIIe au XXe siècle
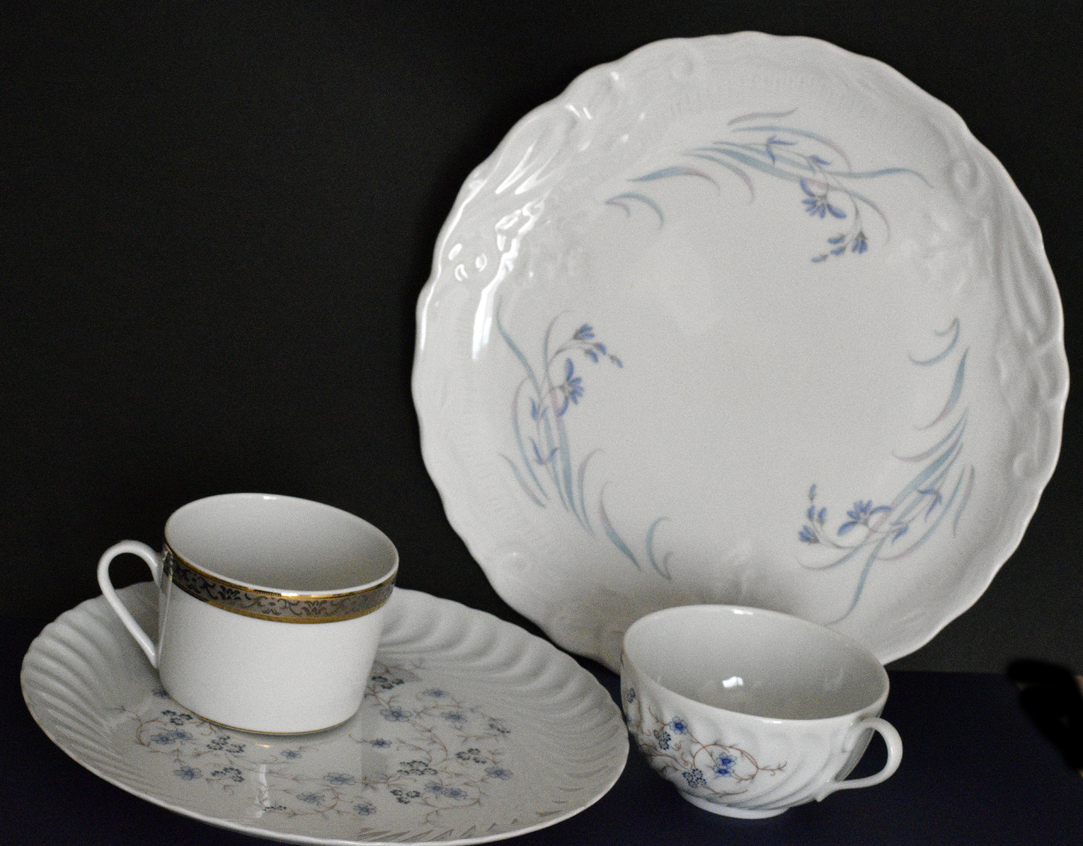
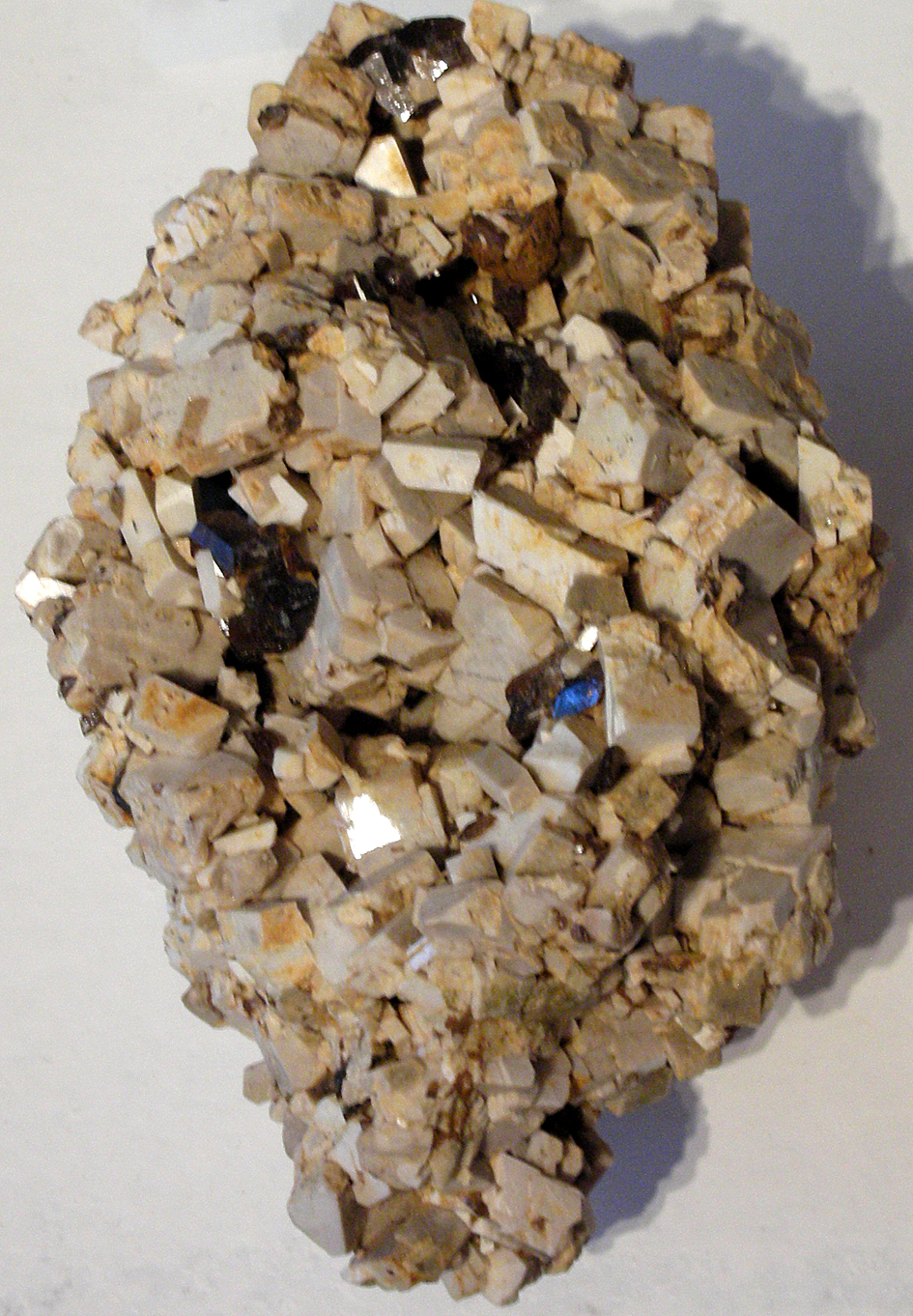
L’origine de la porcelaine
L ‘utilisation du kaolin pour produire la porcelaine chinoise est maitrisée en 1710 par les allemands en Saxe. A partir de cette période, le kaolin entre dans la fabrication des porcelaines en Europe. Le kaolin est exploité en France, à partir de 1765 notamment grâce aux gisements de Saint-Yrieix-la-Perche (Haute-Vienne). Les premières porcelaines sortent de la manufacture de Sèvres en 1767, puis des fabriques de Limoges à partir de 1771.
La porcelaine est obtenue par un mélange finement broyé d’une argile, la kaolinite Al2(Si2O5)(OH)4, de feldspath potassique K(AlSi3O8) et de quartz (SiO2).
Les gisements de kaolin, dont est issue la kaolinite, résultent d’une altération des roches magmatiques, en particulier certains granites. Cette dégradation peut avoir deux origines : l’action d’une solution hydrothermale acide à basse température ; en climat tropical humide, la formation de sédiments issus du lessivage, du transport et du dépôt d’argiles provenant de l’altération de la roche-mère.
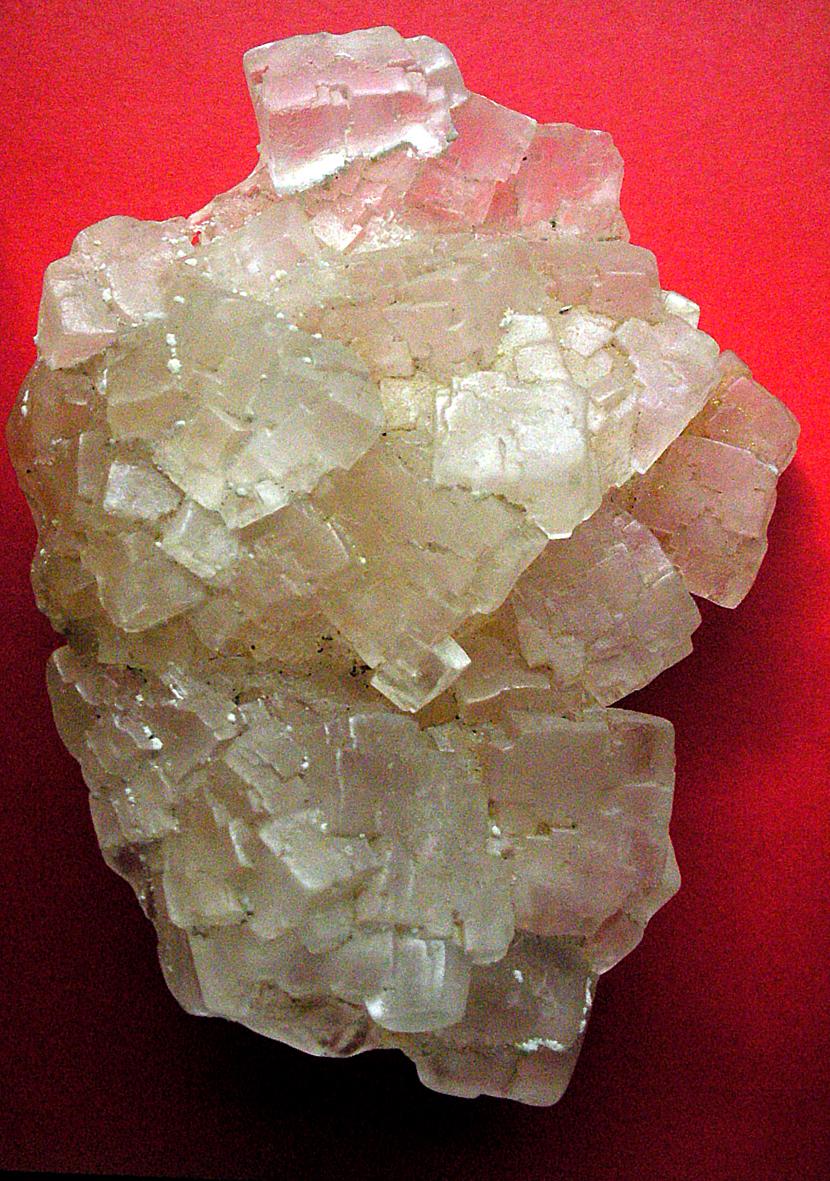
La fertilisation des sols et l’essor de l’agriculture au XIXe siècle
Depuis plusieurs siècles, les Hommes utilisent les matériaux naturels comme certaines roches ou certains minéraux pour reminéraliser les sols mais aussi pour en réguler l’acidité. Le « chaulage » est un exemple de procédé qui permet de reminéraliser les sols. Il consiste à apporter des amendements calciques (CaO, Ca(OH)2) ou calcaires (CaCO3) pour corriger l’acidité des sols agricoles.
La reminéralisation des sols par apport de poudre de roche, de roche broyée, voire de scories silicatées, se développe notamment dans les pays tropicaux (Australie et Brésil). Dans ces pays, les sols sont très fortement altérés et les éléments alcalins et alcalino-terreux ont été lixiviés, c’est-à-dire éliminés par action de l’eau. Des roches comme des basaltes, des carbonates ou des sous-produits de l’activité industrielle riches en minéraux vont s’altérer dans les sols acides tropicaux. Cette dégradation entraîne la libération d’éléments chimiques, notamment les alcalins (le sodium et le potassium) et alcalino-terreux (le calcium) rendus ainsi disponibles pour la végétation.
Les engrais phosphatés, issus principalement de la roche mère phosphatée (par exemple les phosphorites du Maroc), sont également fortement utilisés en agriculture, mais sont connus pour être une source de polluants métalliques et radioactifs. Ils contiennent en particulier de l’uranium. Ils participent à la contamination des sols.
La végétation a également besoin de potassium. La sylvite (KCl, chlorure de potassium), exploitée autrefois dans la plaine du Rhin, est utilisée comme fertiliseur. Lors de l’évaporation de l’eau de mer, la halite (NaCl, chlorure de sodium) précipite en premier avant la sylvite.
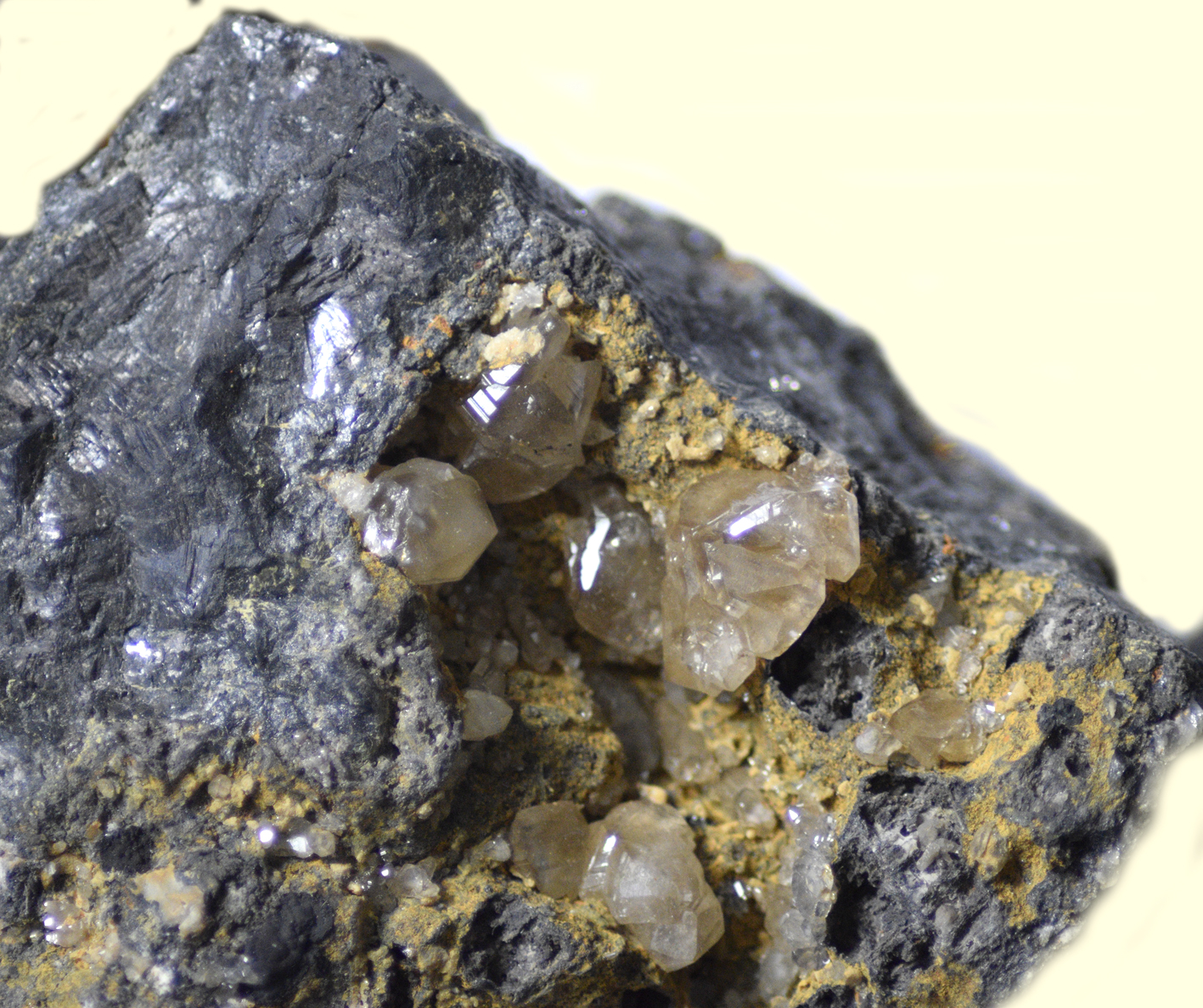
Les pigments issus de la chimie moderne
Le développement de la chimie au XIXe siècle permet de remplacer l’essentiel des pigments minéraux naturels par des pigments minéraux de synthèse très stables et moins onéreux. Ainsi, l’outremer a été synthétisé par J.-B. Guimet en 1826 et remplace l’outremer naturel.
La cérusite (PbCO3), donnant le blanc traditionnel au plomb, est synthétisée au XIXe siècle, mais sa toxicité élevée signe l’arrêt de sa production. Le blanc de zinc (ZnO) est désormais produit, ainsi que le blanc de titane (TiO2) fabriqué à partir de gisement d’anatase et de rutile.
Le bleu de Berlin, un ferrocyanure (C18Fe7N18) hydraté, est synthétisé dès le XVIIIe siècle. L. Gay Lussac en détermine la composition précise en 1811. Vers 1830, il est fabriqué sous le nom de bleu de Prusse ou bleu de cobalt (CoO.Al2O3) plus clair que le bleu de Prusse. C’est ainsi qu’on les trouve après 1830 dans toutes les séries d’estampes japonaises en remplacement des bleus d’origine végétale instables à la lumière.
Il en est de même des pigments jaunes au plomb très toxiques qui sont remplacés par la synthèse du jaune de chrome, de zinc ou de cadmium.
Le vermillon, issu du mercure et du soufre est remplacé par du rouge de cadmium synthétique.
L’arséniate de cuivre, lui aussi très toxique, qui donne le « vert Véronèse » est aussi synthétique. Les principaux verts actuels sont des oxydes de chrome mais il existe aussi le vert de chrome qui est obtenu par un mélange de jaune de chrome et de bleu de Prusse.
Les pigments sont d’excellents marqueurs de leur époque. Leur identification aide dans le processus d’authentification d’œuvres. Des techniques telles que la microscopie électronique à balayage ou la fluorescence X sont ainsi couramment utilisées pour l’analyse de peintures décoratives.
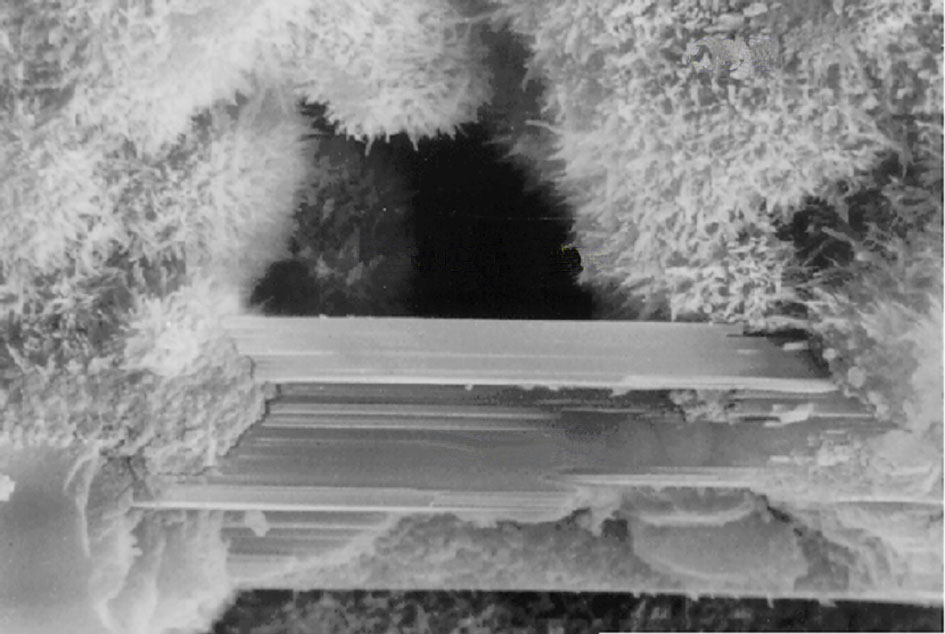
Les ciments modernes
Il faut un siècle aux savants français et anglo-saxons comme Vicat, Le Châtelier, Michaelis ou encore Rankin, pour décrypter « le secret » des ciments et bétons romains. Ils établissent les réactions minéralogiques qui se produisent pendant la fabrication du ciment et sa prise hydraulique. L’industrie des bétons naît et modifie en conséquence la construction et l’architecture vers la fin du XIXème siècle.
La fabrication des ciments est mise au point en étudiant le système des trois oxydes fondamentaux : SiO2, CaO et Al2O3. La réaction qui se déroule à 1455°C conduit à la formation de silicates et aluminates calciques comme l’alite (Ca3OSiO4), la bélite (Ca2SiO4) et l’aluminate tricalcique (Ca3OAl2O5).
On part d’un mélange de calcaire marneux auquel on fait subir une cuisson progressive en 4 étapes dans un four rotatif :
Four de cuisson
- Déshydratation avant 700°C
- Calcination vers 950°C (départ du CO2)
- Cuisson transitionnelle entre 1000 et 1400°C (la chaux est déstabilisée au profit des silicates de chaux)
- Cuisson finale avec début de fusion entre 1400 à 1455°C.
Schéma des étapes de fabrication du ciment
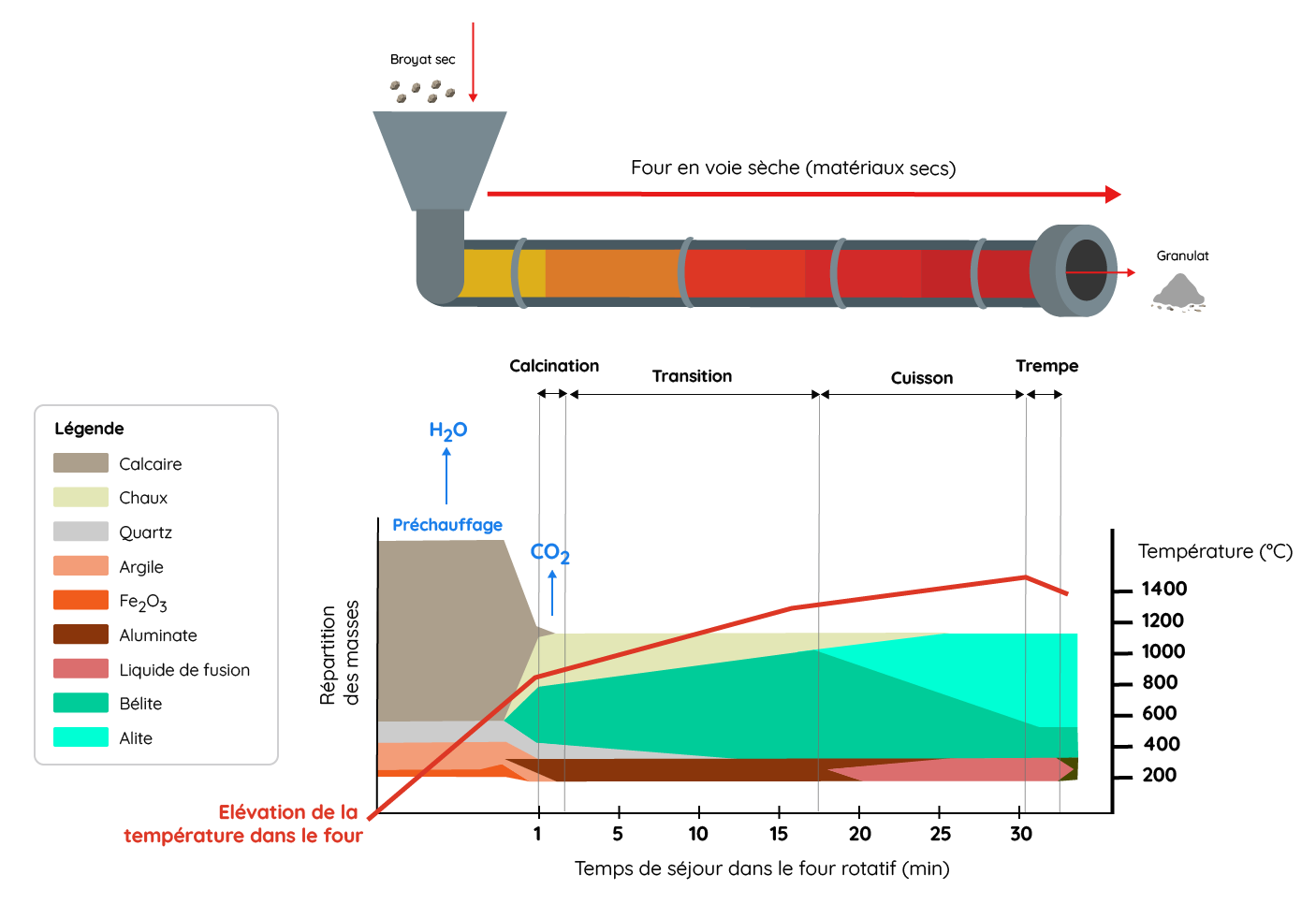
Le mélange de calcaire, d’argile, de silice et d’oxyde de fer appelé cru, est broyé et préchauffé pour le déhydrater puis trois étapes se succèdent dans le four rotatif: la calcination qui est une décarbonation (rejet du CO2), la transition durant laquelle la chaux (CaO) réagit avec la silice (SiO2) et l’alumine (Al2O3) pour former le silicate bicalcique et des aluminates calciques, la cuisson au sens stricte pendant laquelle le silicate tricalcique se forme tandis qu’un début de fusion partielle commence autour de 1400 – 1450°C. Le refroidissement en fin de cuisson donne des granules centimétriques : le clinker qui, broyé, donne le ciment ordinaire appelé ciment portland (composition moyenne : SiO2-21%, Al2O3-5.5%, CaO-65%; Fe2O3-2.5%, MgO-1.5%). L’hydratation du ciment de portland provoque la formation de portlandite (Ca(OH)2) qui participe à la recristallisation du ciment et à son durcissement.
La prise du ciment avec l’eau forme des hydrates. Elle se réalise plus ou moins lentement. La composition finale est quasiment atteinte au bout d’un mois. L’addition d’un sulfate au ciment, comme l’addition de gypse ou d’anhydrite, permet de ralentir les réactions par formation d’un minéral transitoire, l’ettringite Ca6Al2(SO4)3(OH)12.26H2O. Le dosage de la proportion d’eau ajoutée est très strict de manière à ce qu’il reste très peu d’eau libre dans les pores du ciment et que la quasi totalité de l’eau ajoutée devienne de l’eau de constitution des hydrates CSH (42% en masse).
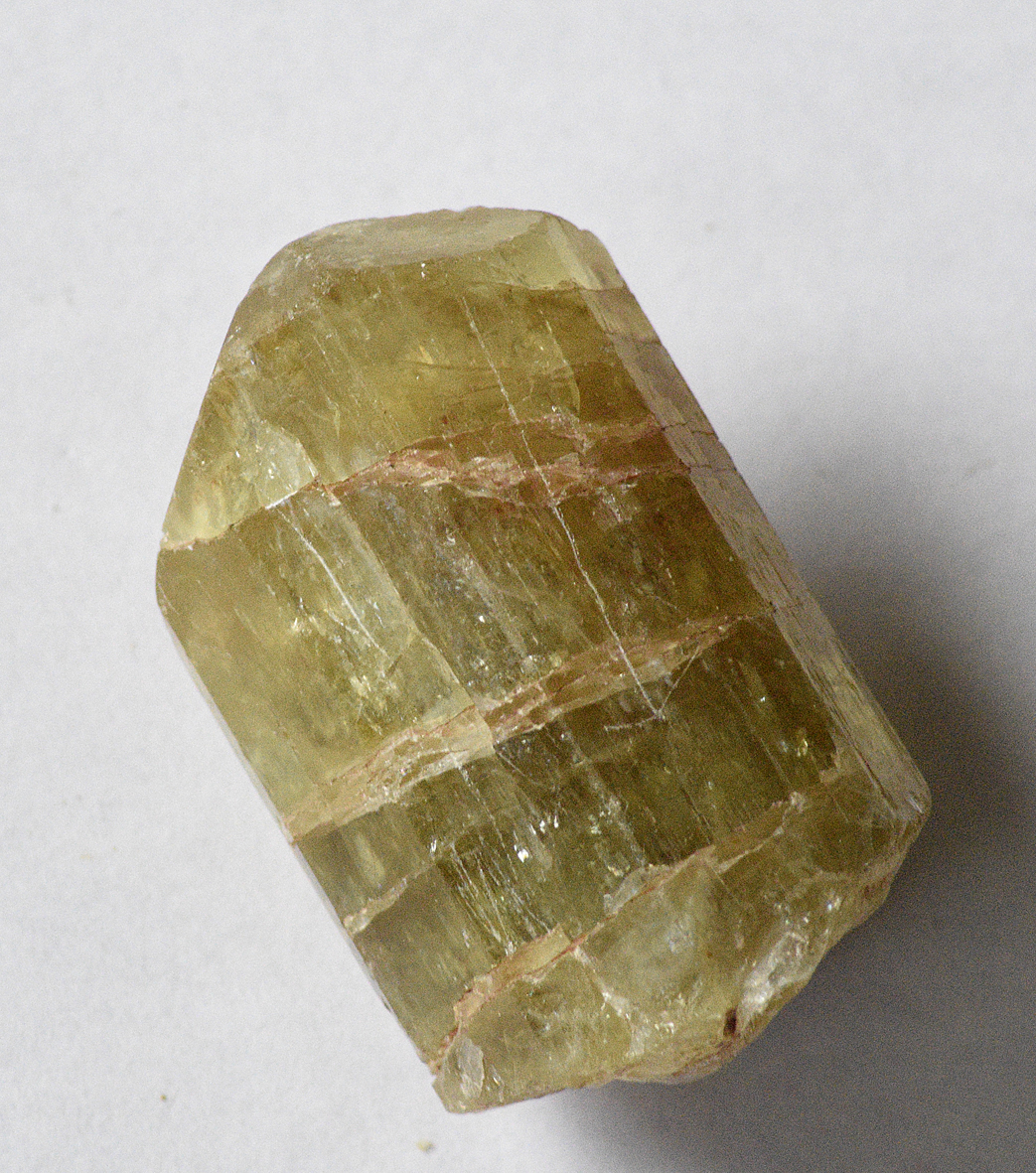
Quelques utilisations courantes
Les minéraux entrent dans la composition de divers produits d’utilisation courante. Une plaquette a été diffusée par la Société de l’Industrie Minérale qui illustre très bien les nombreux domaines économiques et industriels dans lesquels les minéraux interviennent.
Les minéraux ne sont pas toujours là où on les attend comme en témoignent les 3 exemples suivants :
Les dentifrices
Le fluor est un agent actif dans de nombreux dentifrices, il permet la formation d’une couche d’émail plus solide (la fluorapatite, Ca5(PO4)3F), moins sensible aux attaques acides qui provoquent des caries. Toutefois, une teneur en fluor trop élevée dans l’eau de consommation courante a pour conséquence une dégradation des dents. Le fluor provient de la dissolution de la fluorite. En France, des réserves importantes sont connues dans le Morvan (6ème réserves mondiales).
Une manière particulière de prospecter les sites de fluorite a été utilisée, car les animaux brouteurs ont les dents noircies dans les zones riches en fluor.
Les matériaux blancs
Les carbonates forment des pigments blancs pour les peintures décoratives, les matières plastiques, les caoutchoucs, ou encore les adhésifs. En fonction de leurs conditions de dépôt et d’altération les carbonates présentent une pureté variable.
L’oxyde de titane quant à lui, possède un très fort pouvoir éclaircissant et une bonne stabilité à la lumière. Il résiste beaucoup mieux que le calcaire dans les PVC. Ceci est très visible à court terme sur la tenue des volets en PVC aux intempéries et à la lumière.
Le papier couché
Le papier couché possède une plus grande capacité d’impression que le papier ordinaire grâce aux minéraux comme la calcite (CaCO3) ou la kaolinite (Al2(Si2O5)(OH)4) déposés sur sa surface. Les liants appliqués permettent d’obtenir une surface lisse. Le papier acquiert alors une certaine porosité et une meilleure sensibilité à l´impression. L’avantage du papier couché de qualité est que l’encre fait moins de tâches que sur un papier classique.